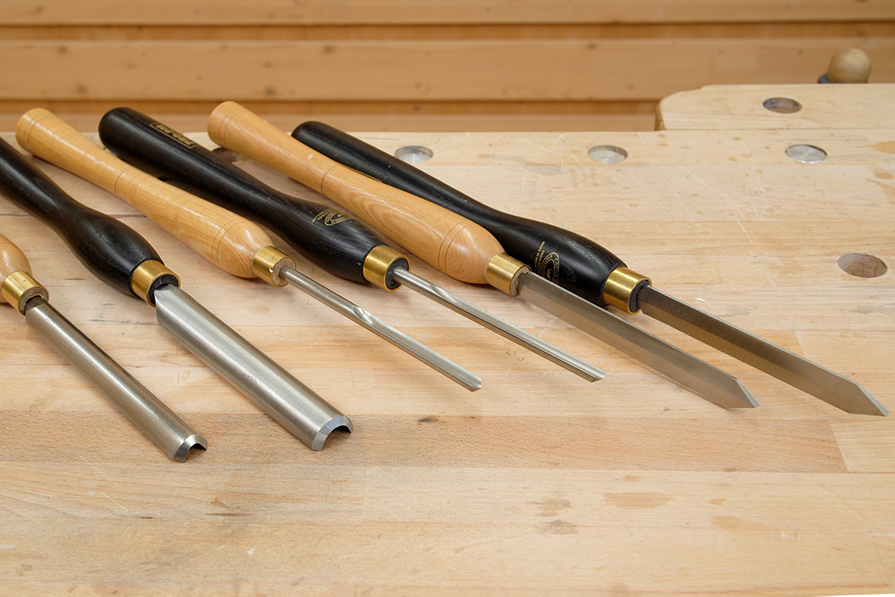
In addition to the intended use of the woodturning tool, for example as a spindle or bowl gouge, scraper and parting tool, the bevel and the shape and length of the handle, it is above all the steel used or its heat treatment that has a major influence on the application of the woodturning tool. We explain the differences between the steels and their properties.
Which HS steels are available for turning gouges?
M2-HSS
High Speed Steel (HSS) is created by alloying chromium, molybdenum, tungsten and vanadium. It is heat-resistant up to approx. 570 °C and highly resistant to abrasion. Most manufacturers of turning tools use the extremely stable M2-HSS for their standard blades. The size of the carbides in the steel structure is up to 12 μm.
M42-HSS
Originally developed to meet the requirements of metal processing, M42 steel cuts even exotic hardwood or composite materials effortlessly. It provides an exceptionally long service life thanks to the addition of 10 % cobalt. There are significantly more carbides in the structure*, which are also very fine (up to 7 μm). This doubles* the tool life and a very fine cutting edge formation.
*compared to standard M2-HSS
What is powder metallurgical steel (PM steel)?
The alloying of steels has its limits due to the different melting points and other properties of the alloying components. In order to create materials that are specifically tailored to the respective application, the technique of »sintering« is used. This refers to a process in which a solid body is created from powdery or granular steel under the influence of high temperature and pressure. This technique produces steels with alloy components that are difficult to mix in the liquid state, such as tungsten alloys.
The alloying elements tungsten and cobalt used for Crown PM steel, for example, provide important properties specifically for woodturning tools. Tungsten (10.5 %) reduces the dulling of cutting edges due to increased heat generation at the tip (friction due to the rotary movement of the workpiece) by a factor of five and makes the turning tool insensitive to dry sharpening on high-speed grinders. Cobalt (8 %) increases the toughness and thus protects the turning tool from breaking, even under the hardest stress.
PM steel is the steel of choice for exotic hardwood, synthetic resin, laminates or wood with mineral inclusions.

M2-HSS, M2-HSS Cryogenic and M42-HSS Cryogenic show clearly recognisable differences in their carbide structure
What are the differences in heat treatment?
Cryogenic hardening is a technically elaborate process, in which after hardening, the steel is cooled down by computer to up to -150 °C. This low temperature treatment usually takes place before tempering and is thus inseparably linked to the hardening process. It gives the steel finer carbides with a size of up to 6 μm, which would not form during normal hardening processes. This results in excellent properties such as a longer service life, a fine cutting edge with reduced burr formation and easier sharpening. »M2-HSS Cryogenic« is used for some Henry Taylor woodturning gouges, for example. Crown uses »M42-HSS Cryogenic« for its high-quality woodturning tools.
How do the types of steel or the different heat treatments differ in sharpening?
It takes longer to sharpen higher alloy steels than standard HSS. However, the longer service life of these turning tools justifies the increased sharpening effort. Many woodturners use a low-speed grinder with a CBN wheel for sharpening their tools. This combination removes material quickly and effectively, so that differences in the steel are less noticeable than with water-cooled grinding.
All the steel types mentioned, including cryogenically hardened steel, can be sharpened on common sharpening systems. For hard steels (HSS and PM), the the Tormek® Blackstone Silicon SB-250 Grinding Wheeand the DICTUM® Black Crystal CBN Grinding Wheels (different versions available, e.g.CBN Black Crystal Grinding Wheel with Circumferential Coating) have proved particularly effective.
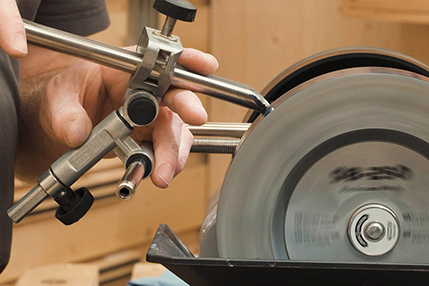
With the appropriate sharpening stone, the Tormek sharpens almost all woodturning tools quickly
One exception is scrapers made of cryogenically hardened steel. Normally, scrapers cut via a burr on the cutting edge. With conventional steels, the burr forms during sharpening, but can also be raised afterwards. Turning tools made of cryogenically hardened steel feature less burr formation, which is quite desirable for gouges, chisels and parting tools. The burr on cryogenically hardened scrapers has to be created in a second work step. However, due to this controlled formation and the fine cutting edge, the burr is very even. Since most woodturners eschew this work step, we only offer our cryogenically hardened DICTUM scrapers on special order.